Guide for cutting
|
|
A: Rotate the saw blade without cutting: Especially when first- time using the new saw blade, the blade should be rotated without cutting for over 30 minutes, and should be used with water in summer hot weather . The purpose is to eliminate the influence of segment to the saw blank during the welding course, and keep high internal quality memory when the saw blades is runing under high speed.
B: The stone block should not be smaller than 0.5m3, and which should be settled steadily in symmetrical position to avoid any vibration.
C: According to the length, width, and height of stone block to adjust the runing switch, the rise and fall of saw blade or the block vehicle should be in valid range. Before the cutting the distance between segment and the highest position of stone block should be 10-20mm. After the cutting the distance between the segment and the bottom of stone block should be 20-40mm. When the cutting of saw blade is changed from left to right or right to left, the blade should be out of stone block completely, the distance should be at least 150-200mm to avoid the strike of blade to the block.
D: The saw blade can only cut the block after steady rotation, when the segment is touching the stone block the saw blade can not be loaded to run(rotate), also when the blade is under cutting in the block the ratation can not be stopped until the blade is out of block completely.
E: Under cutting if find the stone block is vibrating, please stop the cutting immediately, only when the block is settled steadily the cutting can be continued. Under cutting the stone block can not be moved freely.
F: Under cutting if find any unnormal low cutting speed or the blade is nipped, it is possible that the strap is sliding or the compaction nuts become less crowded or the cutting depth is too much or the feed speed is too fast, which concerned should be adjusted in time.
G: The leaner speed should be adapted to the hardess and the type of abrasive of stone, we suggest the following leaner speed according to different type stone.
According to the above expressions, we recommend the following sheet for your reference:
|
|
THE RELATIONS BETWEEN DIAMETER AND RPM
|
DIAMETER
(MM)
|
Leaner Speed (m/s)
|
25
|
30
|
35
|
40
|
45
|
50
|
55
|
RPM of Main Motor (r/min)
|
200 mm
250 mm
300 mm
350 mm
400 mm
450 mm
500 mm
550 mm
600 mm
700 mm
800 mm
900 mm
1000 mm
1100 mm
1200 mm
1300 mm
1400 mm
1500 mm
1600 mm
1800 mm
2000 mm
2200 mm
|
2390
1910
1590
1360
1190
1060
960
870
800
680
600
530
480
430
400
370
340
320
300
270
240
210
|
2870
2290
1910
1640
1430
1270
1150
1040
960
820
720
640
570
520
480
440
410
380
360
330
290
250
|
3340
2670
2230
1910
1670
1490
1340
1220
1110
960
840
740
670
610
560
510
480
450
420
380
330
300
|
3820
3060
2550
2180
1910
1700
1530
1390
1270
1090
960
850
760
690
640
590
550
510
480
440
380
350
|
4300
3440
2870
2460
2150
1910
1720
1560
1430
1230
1070
960
860
780
720
660
610
570
540
490
430
380
|
4780
3820
3180
2730
2390
2120
1910
1740
1590
1360
1190
1060
960
870
800
740
680
640
600
550
480
430
|
5250
4200
3500
3000
2630
2330
2100
1910
1750
1500
1310
1170
1050
960
880
810
700
660
600
530
480
|
|
|
H: Feed Speed, this is depend on the perforamnce of cutting tools usually means the quality of segment. every type tool when the cutting depth is confirmed then the feed speed has its own range. If the speed is too high, then the diamond of segment will be exhausted quickly even fall form the bond, then the life of the segment will be short. If the speed is too low, then the blade’s sharp-self course can not be conducted normally so that the blade become blunt to lose cutting ability. As usual, the feed speed should be slow when the blade enter the cutting, and average when it is cutting. Regarding normal typical material, when the cutting depth is 6mm, we recommend the following list of feed speed for your reference, when the thickness is changing, the cutting speed can be calculated with cutting area(cm2/min).
Please note: The feed speed of initial cutting or the first three cutting course of every piece slab should be half of usual speed.
|
|
FEED SPEED OF COMMON MATERIAL (Unit: mm/min)
|
Material Name
|
GRANITE
|
MARBLE
|
CONCRETE
|
CORUNDUM
|
FEED SPEED
|
500-800
|
2000-3000
|
500-700
|
70-125
|
|
|
I: Regarding the cutting depth of medium hard stone such as marble, limestone which can be cut out one time, as to hard or abrasive stone such as granite, sandstone which should be cut for more times. By using single blade to cut granite, as usual the cutting depth is 4-8mm, cut marbel the cutting depth is 15-30mm, multi-blades two sides cut hard granite, the cutting depth is 3-5mm, anyhow, the cutting depth should be decided by the the hardness of stone, the performance of saw blade and cutting machines.
J: If the rotation direction of the saw blade is same as the movement direction of stone, we call it same-direction-cutting, otherwise we call it contradict-direction-cutting. When the cutting is under contrary direction, there is a rising vertical strength which makes a trend of lifting up the stone block. So, in order to make the block steady, under same cutting conditions, should try to use same-direction-cutting. When under contradict-direction-cutting the cutting depth should be reduced, as usual it should be 1/3-->1/2 of same-direction-cutting depth.
K: Sum up the above mentioned, the basical requirement of cutting technics is: regarding soft hard for easy cutting stone, the cutting can be slow with deep cutting depth, as to the hard stone the cutting is just contrary. To the same type stone and corresponding cutting machine & saw blade, the cutting parameter should be subjected to high efficiency, good quality slab, long life of segment and saw blade, this four points is relevant. When the cutting speed of the saw blade can not keep in a certain number, this means the blade is blunt, should reduce the cutting depth and increase the feed speed to make the blade sharp.
L: Recommended cutting technics of Multi-blades for reference:
|
|
Technics | Material
|
Soft Marble
|
Hard Marble
|
Soft Granite
|
Medium Hard Granite
|
Hard Granite
|
Leaner Speed (m/s)
|
45-50
|
40-50
|
35-40
|
30-35
|
25-30
|
Cutting Depth (mm)
|
300
|
300
|
4-5
|
3-4
|
1-2
|
Feed Speed (mm/min)
|
120-140
|
60-70
|
60
|
60
|
60
|
|
Here is some advice for using core drill bits.TOP Diamond Tools wish you smooth work.
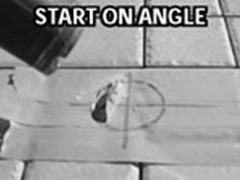 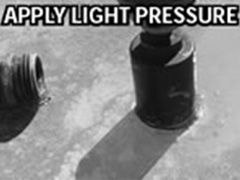
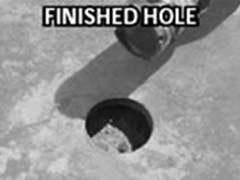
|